Why is invar steel called the most difficult material in the history of laser welding


Why is invar steel called the most difficult material in the history of laser welding
In 1896, the French physicist of invar steel unexpectedly found that the ferronickel alloy composed of 36% nickel, 63.8% iron and 0.2% carbon had abnormal thermal expansion. In the
temperature range below 230 ℃, the size of this alloy material hardly changed with the change of temperature.
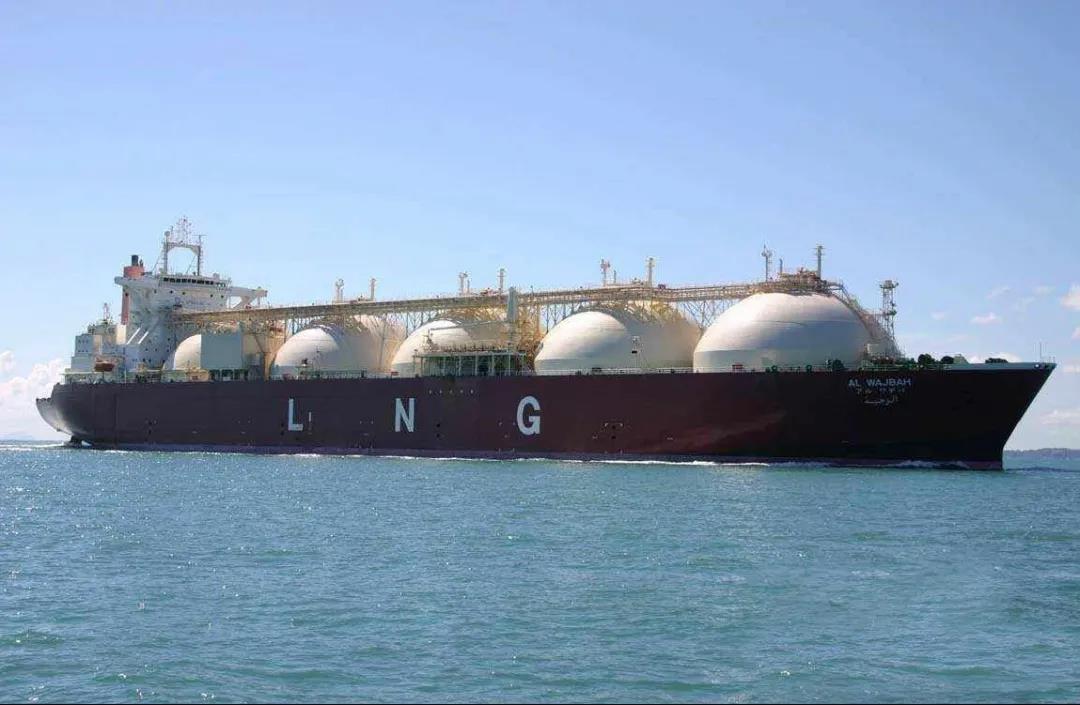
Invar steel is mainly used for LNG transportation
At present, tungsten argon arc welding is generally used for welding of invar steel. This process has large heat input, large workpiece deformation and heat affected zone, and is easy
to produce thermal cracks, which is difficult to ensure the strength of welded joints. Compared with the above methods, laser welding has the advantages of high focus spot density,
small heat input, narrow weld, small heat affected zone, small welding deformation and fast welding speed. Therefore, it is very suitable for the welding of invar steel with large hot
crack tendency.
Laser welding is one of the development directions of invar steel sheet welding, but the concentration of laser energy will produce a large temperature gradient in the welding process,
resulting in large welding stress and affecting the strength of the welded joint. Therefore, from the point of view of reducing the welding temperature gradient, the local preheating
double beam laser welding method of invar steel is proposed: the double beam is obtained by spectroscopic method, the first laser is preheated, the second laser is welded, and the
preheating and welding are carried out simultaneously.
The double light method is used to reduce the welding temperature gradient to improve the strength of the welded joint, which provides an experimental basis for realizing the
high-strength welding of invar steel.