The application of lasers in battery separators cutting


A battery separator refers to a layer of separator material between the positive and negative electrodes of a battery, which is a crucial part of the battery and has a direct impact on the safety and cost of the battery. Its main function is to isolate the positive and negative electrodes and prevent electrons from freely passing through the battery, allowing ions in the electrolyte to freely pass between the positive and negative electrodes. The ion conductivity of the battery separator is directly related to the overall performance of the battery. Its role in isolating the positive and negative electrodes allows the battery to limit the increase in current in the event of overcharging or temperature rise, preventing explosions caused by battery short circuits. It has a microporous self-closing protection effect and provides safety protection for battery users and equipment.
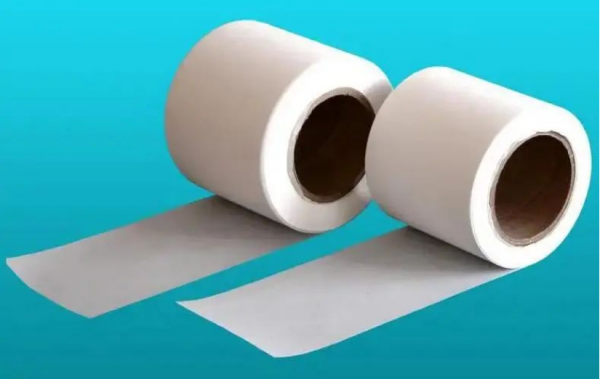
The battery separator is generally produced as a large-area thin film and cannot be directly used in battery production. It needs to be cut according to the required size before it can be applied in battery production. The cutting method is as follows:
Both hot cutting and cold cutting, traditional methods of cutting thin films, are contact cutting. As a result, the diaphragm may have defects such as surface ceramic detachment, cross section drawing, and burrs. Excessive ceramic accumulation into particles can increase the risk of battery short circuits and ultimately lead to safety accidents.
In response to the shortcomings of traditional battery separator cutting methods, a new laser cutting technology is adopted. Through non-contact cutting, the cross-section of the separator can be achieved without burning, carbonization, or melting, thereby improving the safety of lithium battery cells.
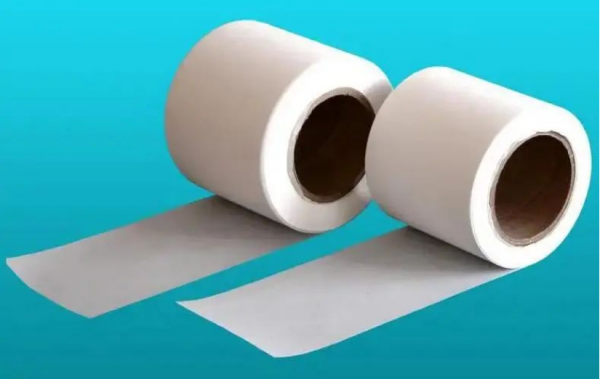
The battery separator is generally produced as a large-area thin film and cannot be directly used in battery production. It needs to be cut according to the required size before it can be applied in battery production. The cutting method is as follows:
Both hot cutting and cold cutting, traditional methods of cutting thin films, are contact cutting. As a result, the diaphragm may have defects such as surface ceramic detachment, cross section drawing, and burrs. Excessive ceramic accumulation into particles can increase the risk of battery short circuits and ultimately lead to safety accidents.
In response to the shortcomings of traditional battery separator cutting methods, a new laser cutting technology is adopted. Through non-contact cutting, the cross-section of the separator can be achieved without burning, carbonization, or melting, thereby improving the safety of lithium battery cells.