Introduction to Plastic Laser Welding Technology


With the energy of laser produces to melt the contact surface of plastics, and then weld the thermoplastic sheet, film and molded components together. It earliest occurred in 1970s, however, due to its high costs, this technology was not competitive by compare with plastic pasting processes, such as vibration welding and hot plate welding. In the middle of 1990s, because of the cost was decreased, laser welding technology is widely used by people.
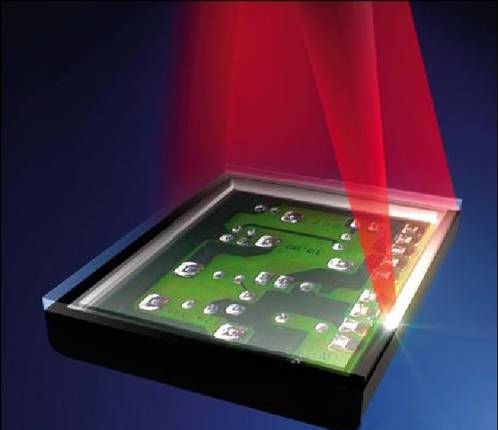
Technics
The most commonly used form of laser welding is called laser transmission welding. The process of this technology involves first clamping two plastic components to be welded together, and then directing a short wave infrared laser to the area to be bonded. The laser beam passes through the upper transparent material and is then absorbed by the lower material. The absorption of laser energy causes the temperature of the lower material to rise, melting the plastic in the upper and lower layers. The upper layer material can be transparent or colored, but it must be able to ensure sufficient laser passage.
Advantages
The advantages of laser welding applied to the fusion of plastic parts include: precision, firmness, and sealing, which are not breathable or leaking, less resin degradation and less debris generated during the welding process, and the surface of the product can be tightly connected around the weld seam. The advantage of laser welding without residue makes it more suitable for pharmaceutical products and electronic sensors regulated by the National Food and Drug Administration.
Easy to control, capable of welding units with small dimensions or complex external structures. Due to the ease of computer software control for lasers, and the flexibility of fiber laser output to reach various subtle parts, laser welding can be used to weld areas that are not easily accessible by other welding methods, welding products with complex shapes, even three-dimensional geometric shapes and five-axes products.
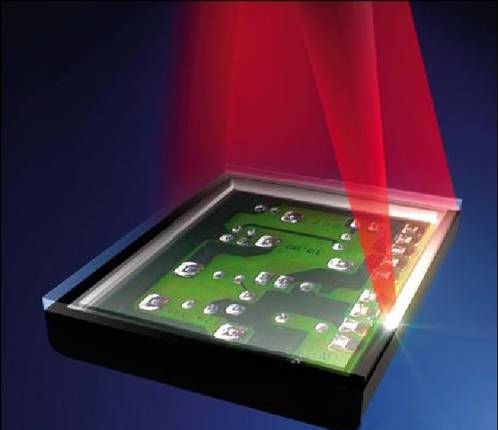
Technics
The most commonly used form of laser welding is called laser transmission welding. The process of this technology involves first clamping two plastic components to be welded together, and then directing a short wave infrared laser to the area to be bonded. The laser beam passes through the upper transparent material and is then absorbed by the lower material. The absorption of laser energy causes the temperature of the lower material to rise, melting the plastic in the upper and lower layers. The upper layer material can be transparent or colored, but it must be able to ensure sufficient laser passage.
Advantages
The advantages of laser welding applied to the fusion of plastic parts include: precision, firmness, and sealing, which are not breathable or leaking, less resin degradation and less debris generated during the welding process, and the surface of the product can be tightly connected around the weld seam. The advantage of laser welding without residue makes it more suitable for pharmaceutical products and electronic sensors regulated by the National Food and Drug Administration.
Easy to control, capable of welding units with small dimensions or complex external structures. Due to the ease of computer software control for lasers, and the flexibility of fiber laser output to reach various subtle parts, laser welding can be used to weld areas that are not easily accessible by other welding methods, welding products with complex shapes, even three-dimensional geometric shapes and five-axes products.