Common problems and solutions in laser welding of aluminum alloys


In daily welding process, due to the special nature of aluminum, laser welding is hard to control the laser focus and welding spool. When the improper parameter is set or lacking of abundant engineering experiences, the air holes, cracks, deformations and black may occur, this seriously influence the welding quality and nature. Now, we are going to introduce the problems and solutions of aluminum laser welding process.
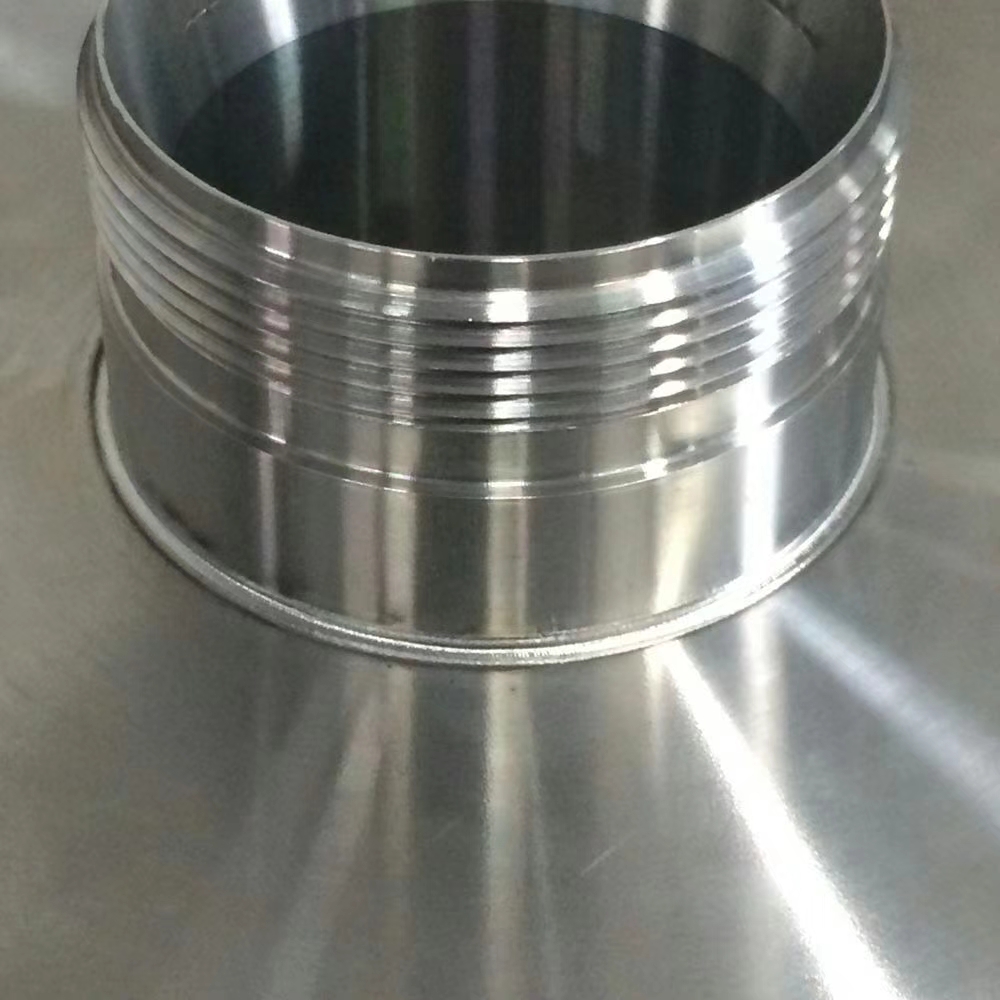
Air holes
When using laser welding of aluminum materials the main problem encountered is air holes. During the welding process, the laser beam causes fluctuations in the welding pool, and when gas trapped in the metal expands and overflows, pores will appear; In addition, aluminum oxide thin films can hinder the bonding between metals, adsorb water and easily generate impurities, promoting the formation of air holes.
The generation of air holes can lead to weak weld strength, reduced corrosion resistance, and unsightly welds. In general, it is recommended to take the following measures:
1. Adjust the appropriate laser power to ensure uniform heat input.
2. When welding thin plates, it is recommended to increase the speed to reduce the time for gas to expand in the metal; When welding thick plates, preheating the material can reduce the welding speed and ensure the performance of the weld seam.
3. Chemical or mechanical cleaning of the weld surface to reduce the impact of impurities on welding quality.
4. Control the use of protective gas or flux to reduce oxidation and reduce the amount of gas formed.
Hot cracking
Due to the high temperature generated during the welding process, aluminum can rapidly expand and contract, resulting in stress points. If the solidification interval of the weld seam is too short and the stress points are not released, they will lead to aluminum cracking and thermal cracking;
Blackening
The blackening of aluminum during laser welding is mainly caused by insufficient laser power, improper defocusing, or damage to the laser lens. In this case, the laser energy failed to reach the melting threshold of the oxide layer on the surface of the aluminum material, causing the aluminum to mix with air and impurities, resulting in blackening of the welding area.
In order to better obtain the quality and aesthetics of welding, it is recommended to first select the appropriate power and set the correct defocus amount during the aluminum welding process; Secondly, you can also check if the protective lenses are damaged.
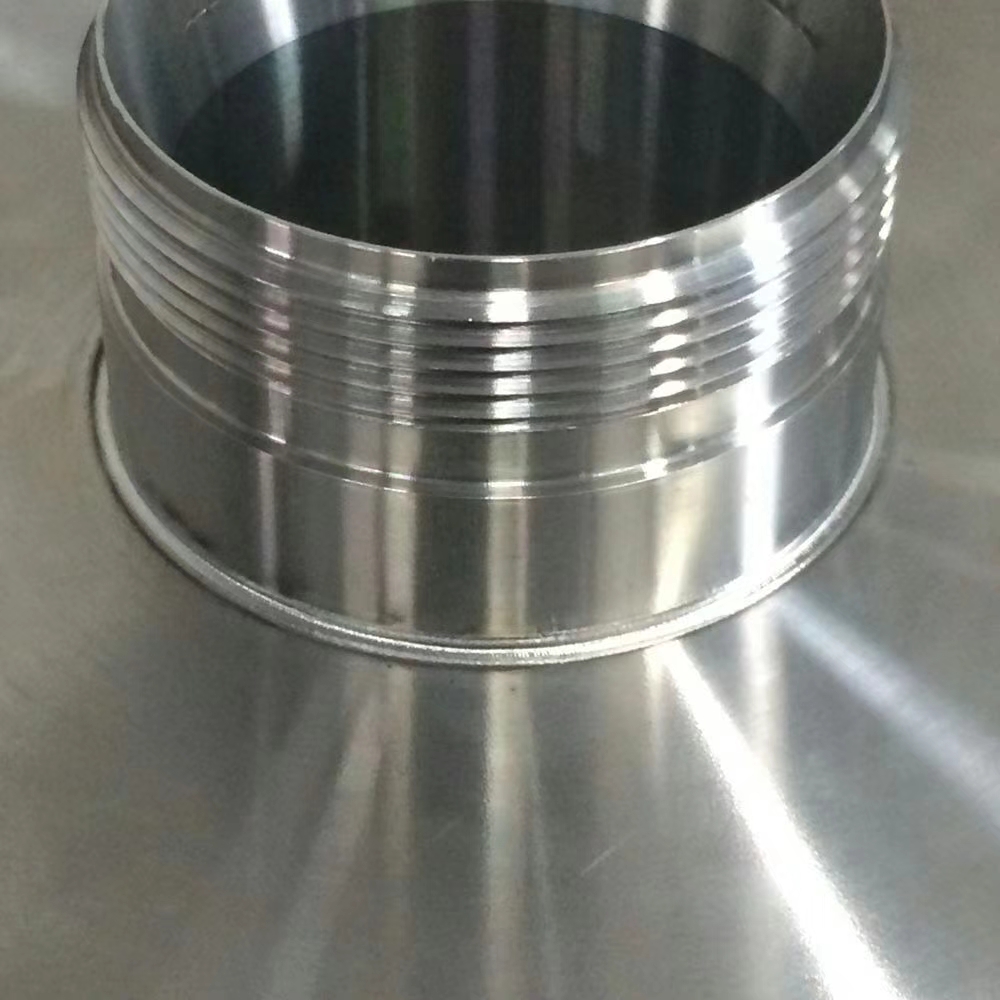
Air holes
When using laser welding of aluminum materials the main problem encountered is air holes. During the welding process, the laser beam causes fluctuations in the welding pool, and when gas trapped in the metal expands and overflows, pores will appear; In addition, aluminum oxide thin films can hinder the bonding between metals, adsorb water and easily generate impurities, promoting the formation of air holes.
The generation of air holes can lead to weak weld strength, reduced corrosion resistance, and unsightly welds. In general, it is recommended to take the following measures:
1. Adjust the appropriate laser power to ensure uniform heat input.
2. When welding thin plates, it is recommended to increase the speed to reduce the time for gas to expand in the metal; When welding thick plates, preheating the material can reduce the welding speed and ensure the performance of the weld seam.
3. Chemical or mechanical cleaning of the weld surface to reduce the impact of impurities on welding quality.
4. Control the use of protective gas or flux to reduce oxidation and reduce the amount of gas formed.
Hot cracking
Due to the high temperature generated during the welding process, aluminum can rapidly expand and contract, resulting in stress points. If the solidification interval of the weld seam is too short and the stress points are not released, they will lead to aluminum cracking and thermal cracking;
Blackening
The blackening of aluminum during laser welding is mainly caused by insufficient laser power, improper defocusing, or damage to the laser lens. In this case, the laser energy failed to reach the melting threshold of the oxide layer on the surface of the aluminum material, causing the aluminum to mix with air and impurities, resulting in blackening of the welding area.
In order to better obtain the quality and aesthetics of welding, it is recommended to first select the appropriate power and set the correct defocus amount during the aluminum welding process; Secondly, you can also check if the protective lenses are damaged.