Han's phtonics assists to upgrade the welding manufacturing in new energy industry


The global automobile market is transforming to electrification as a whole. Laser welding has become a very important process in the manufacturing of new energy automobile parts, body and power battery.
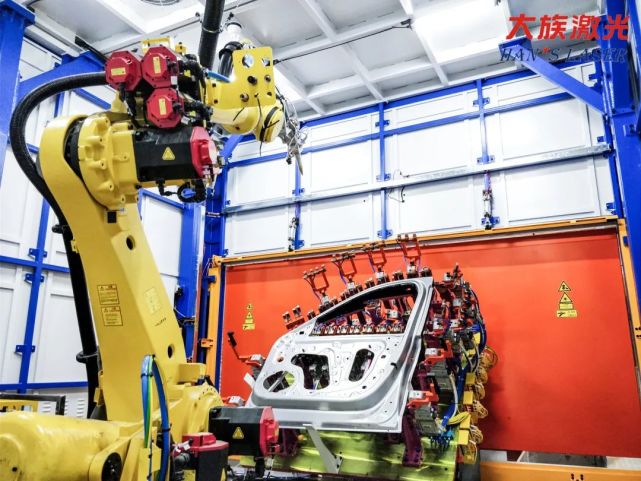
Advantages of laser welding
1. Improve production efficiency
Laser welding is easy to realize production automation, with high welding precision and speed, 3-5 times faster than traditional welding, which can significantly improve production efficiency.
2. No post processing required
Laser can perform small-scale local precision welding, and the surface of the product is smooth and flat, without the need for post processing.
3. Non-contact machining with low loss
Laser welding technology belongs to non-contact welding, which has very little impact on the loss and deformation of the machine, and the equipment maintenance cost is low.
4. Wide welding application range
It can meet the free combination welding of different materials, reduce material usage, and assist in the lightweight of automobiles.
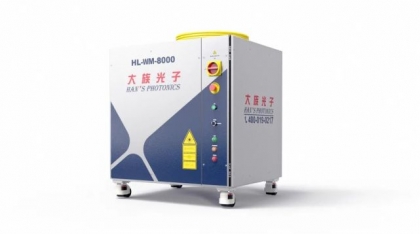
Welding of vehicle body and components
1. Self-fusion welding
Self-fusion welding forms a weld seam by laser melting of the base material, no need to add filler materials such as welding wires in the middle. The automobile A pillar, B pillar and D pillar are made of thermoforming high-strength steel, which are designed as hydroforming profiles. Overlay welding and tailor welded joints are adopted, which can only be welded from one side. It is more flexible to use laser self-fusion welding.
Selecting the Han’s photonics HL-WM-8000 fiber laser, with high welding accuracy and beautiful appearance; Less welding consumables, reducing production costs; Flexible and convenient operation, which can improve the obstacle angle of A-pillar, reduce weight, and improve safety; The laser welding speed is up to 2-4m/min, which effectively improves the welding efficiency.
2. Arc composite welding
Arc composite welding is an emerging special laser processing technology that combines laser and arc heat sources, creating a synergistic effect between the two. It has the advantages of both heat sources, compensates for shortcomings, and forms a low-cost and highly adaptable welding method. The material of the car chassis is high-strength steel, which adopts a laser arc composite welding process. The preparation before welding is reduced, the welding seam bridging ability is enhanced, and the beam utilization rate is improved.
Selecting Han’s photonics HL-WM-4000 fiber laser, with high electro-optical conversion efficiency and energy saving; High welding efficiency, with an average speed of 2m/min; The welding process is aesthetically pleasing and flat, with minimal deformation of the workpiece, small heat affected zone, and small softening zone; Permissible welding gaps of ≤ 2mm and plate misalignment of ≤ 1mm.
3. Flight welding
Flying welding is a new type of laser welding technology that uses a robot to control the laser galvanometer for scanning welding. Through the close cooperation between the robotand the laser galvanometer, the robot has zero contact with the workpiece in the welding process, and the weld position is flexible and changeable. With professional graphics processing software, three-dimensional space instantaneous multi-track welding is realized. Flight welding is mainly applied to car seat panels, door structural components, etc., greatly reducing positioning time. Combining the advantages of remote welding, galvanometer, and robots, it maximizes the online time of the laser beam and greatly improves production efficiency.
Selecting a large family of photon HL-WM-6000 fiber laser, with stable power output; Good beam quality and controllability; High welding accuracy can effectively reduce the number of welding points and save costs; Adapt to any weld form and direction, with uniform distribution of welds/points; The equipment occupies a small area and has low maintenance costs.
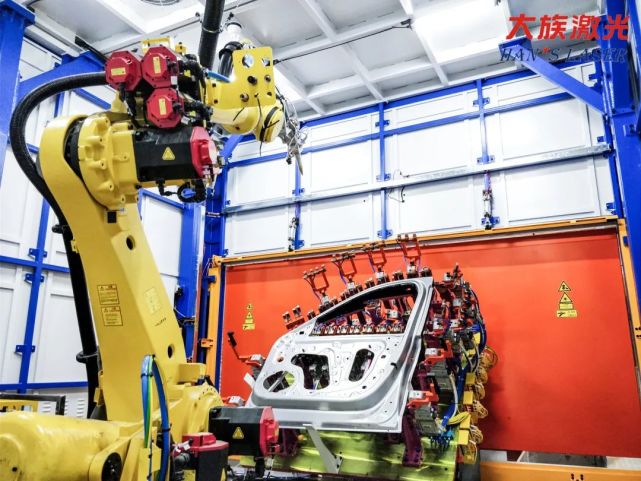
Advantages of laser welding
1. Improve production efficiency
Laser welding is easy to realize production automation, with high welding precision and speed, 3-5 times faster than traditional welding, which can significantly improve production efficiency.
2. No post processing required
Laser can perform small-scale local precision welding, and the surface of the product is smooth and flat, without the need for post processing.
3. Non-contact machining with low loss
Laser welding technology belongs to non-contact welding, which has very little impact on the loss and deformation of the machine, and the equipment maintenance cost is low.
4. Wide welding application range
It can meet the free combination welding of different materials, reduce material usage, and assist in the lightweight of automobiles.
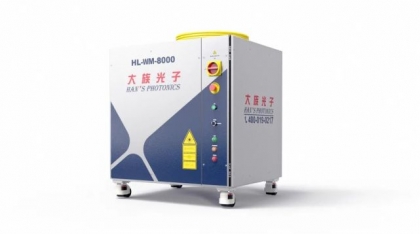
Welding of vehicle body and components
1. Self-fusion welding
Self-fusion welding forms a weld seam by laser melting of the base material, no need to add filler materials such as welding wires in the middle. The automobile A pillar, B pillar and D pillar are made of thermoforming high-strength steel, which are designed as hydroforming profiles. Overlay welding and tailor welded joints are adopted, which can only be welded from one side. It is more flexible to use laser self-fusion welding.
Selecting the Han’s photonics HL-WM-8000 fiber laser, with high welding accuracy and beautiful appearance; Less welding consumables, reducing production costs; Flexible and convenient operation, which can improve the obstacle angle of A-pillar, reduce weight, and improve safety; The laser welding speed is up to 2-4m/min, which effectively improves the welding efficiency.
2. Arc composite welding
Arc composite welding is an emerging special laser processing technology that combines laser and arc heat sources, creating a synergistic effect between the two. It has the advantages of both heat sources, compensates for shortcomings, and forms a low-cost and highly adaptable welding method. The material of the car chassis is high-strength steel, which adopts a laser arc composite welding process. The preparation before welding is reduced, the welding seam bridging ability is enhanced, and the beam utilization rate is improved.
Selecting Han’s photonics HL-WM-4000 fiber laser, with high electro-optical conversion efficiency and energy saving; High welding efficiency, with an average speed of 2m/min; The welding process is aesthetically pleasing and flat, with minimal deformation of the workpiece, small heat affected zone, and small softening zone; Permissible welding gaps of ≤ 2mm and plate misalignment of ≤ 1mm.
3. Flight welding
Flying welding is a new type of laser welding technology that uses a robot to control the laser galvanometer for scanning welding. Through the close cooperation between the robotand the laser galvanometer, the robot has zero contact with the workpiece in the welding process, and the weld position is flexible and changeable. With professional graphics processing software, three-dimensional space instantaneous multi-track welding is realized. Flight welding is mainly applied to car seat panels, door structural components, etc., greatly reducing positioning time. Combining the advantages of remote welding, galvanometer, and robots, it maximizes the online time of the laser beam and greatly improves production efficiency.
Selecting a large family of photon HL-WM-6000 fiber laser, with stable power output; Good beam quality and controllability; High welding accuracy can effectively reduce the number of welding points and save costs; Adapt to any weld form and direction, with uniform distribution of welds/points; The equipment occupies a small area and has low maintenance costs.