Laser cleaning: a popular application in lithium battery manufacturing


As a new green "Black Tech", laser cleaning has always been one of the research hotspots in the field of industrial manufacturing. With the vigorous development of the new energy industry, the demand for lithium batteries has increased sharply, which also poses new tasks and challenges to the cleaning process in lithium battery manufacturing. In the past two years, under the strong promotion of the head laser enterprises, laser cleaning has been widely used in the manufacturing process of new energy batteries, and has moved from an industrial substitute to a dominant stage.
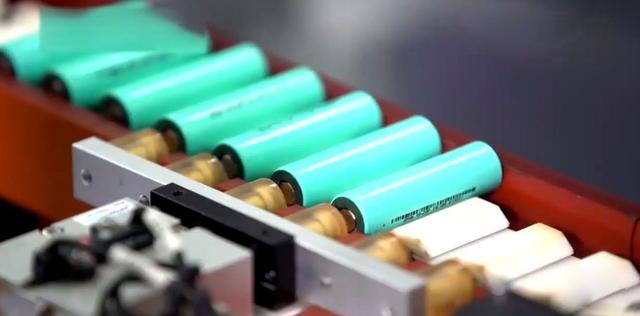
Electrode cleaning
In the lithium-ion battery manufacturing process, before the electrode lug is welded, the coating in the area of the electrode lug to be welded needs to be cleaned to ensure the stability of the current collector in the battery. The methods of removing coating mainly include mechanical scraping, chemical cleaning and laser cleaning. Among them, mechanical scraping and chemical cleaning have weaknesses such as regular shutdown and replacement of consumables, easy to damage the pole piece, and difficult to ensure the cleaning of the coating.
Cleaning of new energy battery shell
The cleanliness of the battery shell is one of the factors that determine the high energy density, service life and safety performance of the power battery. However, when processing the new energy power battery shell, the drawing oil with high viscosity will be used to protect the surface of the workpiece from damage, but the drawing oil with high viscosity will cause serious oil pollution on the surface of the battery shell, and the carbon deposition and sintering caused by high temperature processing, it will make the surface of the workpiece extremely difficult to clean.
As a new type of green cleaning technology, laser cleaning is different from chemical cleaning and dry ice cleaning. The cleaning method is green and environmentally friendly, and the cleanliness is high. It can effectively remove carbon deposits, oil stains, metal chips and other stains on the surface of the workpiece, and the surface is free of scratches and burrs after cleaning, thus improving the safety performance and service life of the power battery.
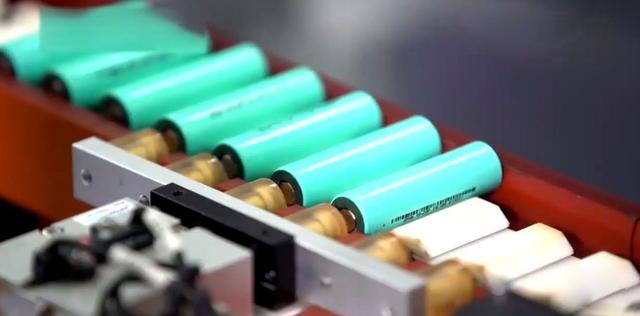
Electrode cleaning
In the lithium-ion battery manufacturing process, before the electrode lug is welded, the coating in the area of the electrode lug to be welded needs to be cleaned to ensure the stability of the current collector in the battery. The methods of removing coating mainly include mechanical scraping, chemical cleaning and laser cleaning. Among them, mechanical scraping and chemical cleaning have weaknesses such as regular shutdown and replacement of consumables, easy to damage the pole piece, and difficult to ensure the cleaning of the coating.
Cleaning of new energy battery shell
The cleanliness of the battery shell is one of the factors that determine the high energy density, service life and safety performance of the power battery. However, when processing the new energy power battery shell, the drawing oil with high viscosity will be used to protect the surface of the workpiece from damage, but the drawing oil with high viscosity will cause serious oil pollution on the surface of the battery shell, and the carbon deposition and sintering caused by high temperature processing, it will make the surface of the workpiece extremely difficult to clean.
As a new type of green cleaning technology, laser cleaning is different from chemical cleaning and dry ice cleaning. The cleaning method is green and environmentally friendly, and the cleanliness is high. It can effectively remove carbon deposits, oil stains, metal chips and other stains on the surface of the workpiece, and the surface is free of scratches and burrs after cleaning, thus improving the safety performance and service life of the power battery.