Uncover the secrets of button battery laser welding, helping the era of intelligent wearing


In recent years, with the explosion of TWS earphones, new rechargeable button batteries with advantages such as high endurance, high safety and personalization have been unprecedentedly popular in various small wearable devices such as TWS earphones, smart watches, smart glasses and smart speakers.
Button cell, also known as button style cell, has the greatest advantage of good consistency and will not bulge during the charging and discharging cycle. It can set a larger battery capacity and directly attach to the PCB.
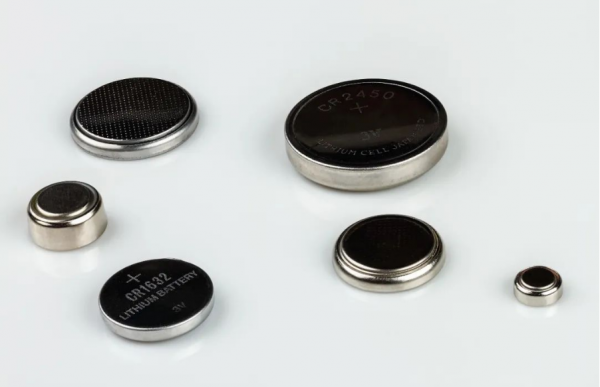
Traditional welding processing technology is difficult to achieve the high standard welding indicators of the new button battery. In contrast, laser welding technology can meet the diversity of button battery processing technology.
For example, welding of different materials (stainless steel, aluminum alloy, copper, nickel, etc.), irregular welding tracks, more detailed welding points, and more accurate positioning welding areas, not only improve the product welding consistency, but also reduce the damage to the battery during the welding process. It is the best welding process for button cell at present.
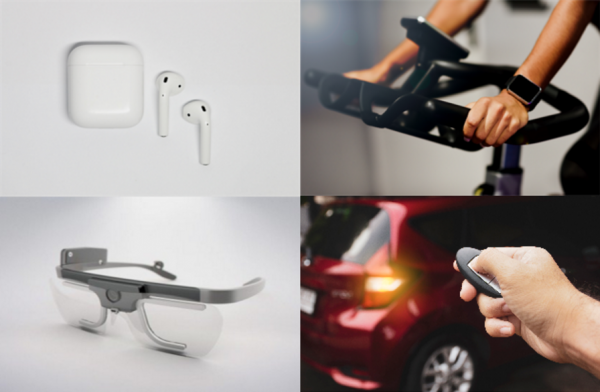
Laser application process of button battery
2. Electric core section: welding the positive and negative poles of the winding core with the shell cover, laser welding the shell cover with the shell, and welding the sealing nails;
3. Module PACK section: electric core screening, side pasting, positive and negative electrode welding, post welding inspection, size inspection, upper and lower adhesive tape, air tightness inspection, blanking sorting, etc.
Difficulties in button battery welding and intelligent assembly
When the positive and negative poles of the coil core are welded with the shell cover, the copper material has good conductivity, but the high reflective material has very low laser absorption rate. In addition, the material is extremely thin, which can easily deform when the heating area is too large, the heating time is too long, or the laser power density is not enough, resulting in poor welding.
When the top cover is sealed and welded, the thickness of the connection between the button battery shell and the cover plate after processing is only 0.1mm, which cannot be realized by traditional welding. If the laser welding power is too high, the battery shell will be directly broken down, and the internal electric core will be damaged, and the material is very easy to deform. If the power is low, the welding pool cannot be formed to achieve the purpose of welding.
Pin and finished battery are usually realized by overlapping penetration welding. During this welding process, the battery has been sealed and filled with electrolyte. If the welding process is unstable, it is easy to cause internal diaphragm welding damage and short circuit, or the battery shell is welded through, resulting in electrolyte outflow, faulty welding, over welding and other undesirable phenomena.
Button cell, also known as button style cell, has the greatest advantage of good consistency and will not bulge during the charging and discharging cycle. It can set a larger battery capacity and directly attach to the PCB.
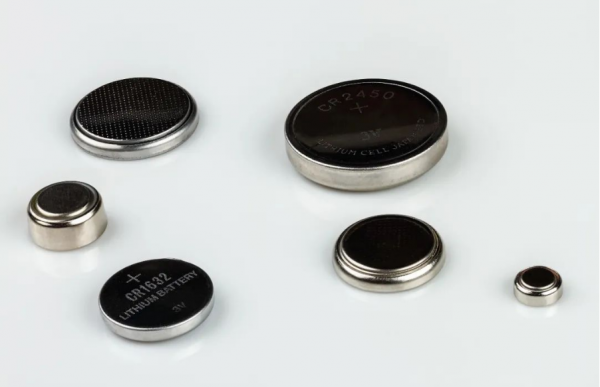
Traditional welding processing technology is difficult to achieve the high standard welding indicators of the new button battery. In contrast, laser welding technology can meet the diversity of button battery processing technology.
For example, welding of different materials (stainless steel, aluminum alloy, copper, nickel, etc.), irregular welding tracks, more detailed welding points, and more accurate positioning welding areas, not only improve the product welding consistency, but also reduce the damage to the battery during the welding process. It is the best welding process for button cell at present.
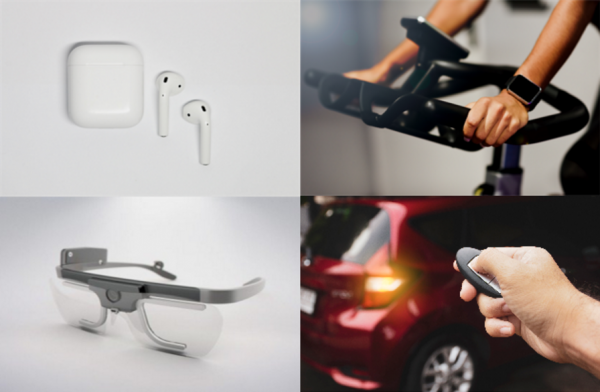
Laser application process of button battery
1. Shell and cover plate: laser etching of button steel shell;
2. Electric core section: welding the positive and negative poles of the winding core with the shell cover, laser welding the shell cover with the shell, and welding the sealing nails;
3. Module PACK section: electric core screening, side pasting, positive and negative electrode welding, post welding inspection, size inspection, upper and lower adhesive tape, air tightness inspection, blanking sorting, etc.
Difficulties in button battery welding and intelligent assembly
When the positive and negative poles of the coil core are welded with the shell cover, the copper material has good conductivity, but the high reflective material has very low laser absorption rate. In addition, the material is extremely thin, which can easily deform when the heating area is too large, the heating time is too long, or the laser power density is not enough, resulting in poor welding.
When the top cover is sealed and welded, the thickness of the connection between the button battery shell and the cover plate after processing is only 0.1mm, which cannot be realized by traditional welding. If the laser welding power is too high, the battery shell will be directly broken down, and the internal electric core will be damaged, and the material is very easy to deform. If the power is low, the welding pool cannot be formed to achieve the purpose of welding.
Pin and finished battery are usually realized by overlapping penetration welding. During this welding process, the battery has been sealed and filled with electrolyte. If the welding process is unstable, it is easy to cause internal diaphragm welding damage and short circuit, or the battery shell is welded through, resulting in electrolyte outflow, faulty welding, over welding and other undesirable phenomena.