Introduction of five laser plastic welding methods


Nowadays, many products (including automotive semiconductor industry, pharmaceutical and food industry, etc.) have very high requirements for processing accuracy and aesthetic appearance, which makes laser welding a necessary process for the production of these products. The closer the compatibility, fusion temperature and matching of plastic laser welding are, the better its effect will be. The application of plastic laser welding is different from metal welding, including sequential perimeter welding, quasi synchronous welding, synchronous welding and irradiation mask welding.
1. Contour welding
The laser moves along the contour of the plastic welding layer and melts it, gradually bonding the plastic layers together; or move the sandwiched layer along the fixed laser beam to achieve the purpose of welding.
2. Synchronous welding
The laser beams from a plurality of diode lasers are shaped by optical elements. The laser beams are guided along the contour of the welding layer, and heat is generated at the weld seam, so that the entire contour is melted and bonded together at the same time.
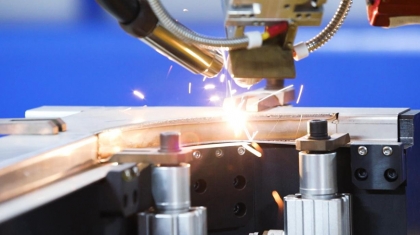
3. Scanning welding
Scanning welding is also known as quasi synchronous welding. Scanning welding technology combines the above two welding technologies: sequential circumferential welding and synchronous welding. The high-speed laser beam generated by the mirror moves along the part to be welded at a speed of 10m / s, so that the whole welding part gradually heats up and fuses together.
4. Rolling welding
Rolling welding is an innovative laser plastic welding process, which has many different forms. There are two main forms of rolling welding:
The first is Globo ball welding. There is an air cushion glass ball at the end of the laser lens. This glass ball can focus the laser and clamp the plastic parts at the same time.
The second is twinweld welding technology. This plastic laser welding technology adds a metal pressure roller at the end of the lens. During the welding process, the pressure roller presses the edge of the welding line for welding.
5. Irradiation mask welding
The laser beam is positioned through the template to melt and bond the plastic. The template only exposes a small area of the precise welding part on the plastic layer below. The laser beam only heats the part of the product that is not covered by the mask. Using this technology, laser can achieve high-precision welding as low as 10 microns.
1. Contour welding
The laser moves along the contour of the plastic welding layer and melts it, gradually bonding the plastic layers together; or move the sandwiched layer along the fixed laser beam to achieve the purpose of welding.
2. Synchronous welding
The laser beams from a plurality of diode lasers are shaped by optical elements. The laser beams are guided along the contour of the welding layer, and heat is generated at the weld seam, so that the entire contour is melted and bonded together at the same time.
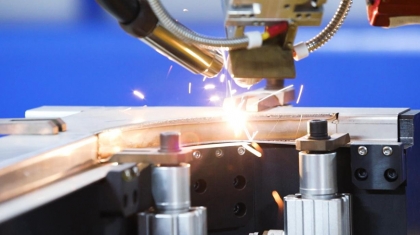
3. Scanning welding
Scanning welding is also known as quasi synchronous welding. Scanning welding technology combines the above two welding technologies: sequential circumferential welding and synchronous welding. The high-speed laser beam generated by the mirror moves along the part to be welded at a speed of 10m / s, so that the whole welding part gradually heats up and fuses together.
4. Rolling welding
Rolling welding is an innovative laser plastic welding process, which has many different forms. There are two main forms of rolling welding:
The first is Globo ball welding. There is an air cushion glass ball at the end of the laser lens. This glass ball can focus the laser and clamp the plastic parts at the same time.
The second is twinweld welding technology. This plastic laser welding technology adds a metal pressure roller at the end of the lens. During the welding process, the pressure roller presses the edge of the welding line for welding.
5. Irradiation mask welding
The laser beam is positioned through the template to melt and bond the plastic. The template only exposes a small area of the precise welding part on the plastic layer below. The laser beam only heats the part of the product that is not covered by the mask. Using this technology, laser can achieve high-precision welding as low as 10 microns.