What if laser cutting burns?


Laser cutting is to focus the laser beam on the surface of the material with a focusing lens to melt the material. At the same time, the compressed gas coaxial with the laser beam is used to blow away the melted material, and make the laser beam and the material move relatively along a certain track, so as to form a certain shape of slit.
Five steps to achieve the purpose of cutting.
1. The laser amplifier emits the laser and focuses on the material surface through the cutting head
2. The material absorbs laser and melts
3. The molten part burns under the combustion supporting effect of oxygen
4. Combustion extends downward along the plate thickness
5. Molten metal is blown out of the slit
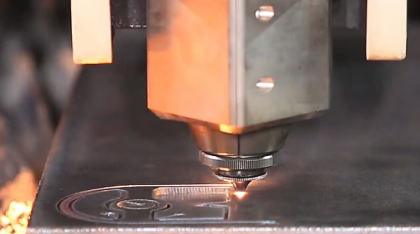
Causes affecting overburning
Material surface
Uneven thickness of film / skin or warping not close to the plate will lead to uneven absorption of laser by the plate, resulting in unstable heat generation.
Heat accumulation
When the machining path involves multiple small-size shapes, the heat will accumulate continuously as the cutting proceeds, and it is easy to burn when cutting to the second half.
Overheat at sharp corners
Overburning at sharp corners is usually caused by heat accumulation, specifically because the temperature at the sharp corners has risen to a high level when the laser passes. If the forward speed of the laser beam is greater than the heat transfer speed, overburning can be effectively avoided.
How to solve over burning?
In general, the heat conduction velocity during overburning is 2m/min, and when the cutting speed is greater than 2m/min, melting loss basically does not occur. Therefore, using high-power laser cutting can effectively prevent overheating.
Five steps to achieve the purpose of cutting.
1. The laser amplifier emits the laser and focuses on the material surface through the cutting head
2. The material absorbs laser and melts
3. The molten part burns under the combustion supporting effect of oxygen
4. Combustion extends downward along the plate thickness
5. Molten metal is blown out of the slit
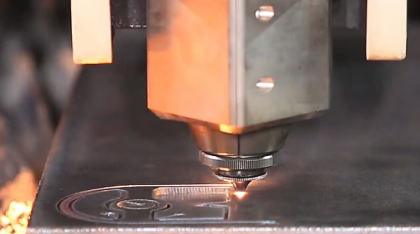
Causes affecting overburning
Material surface
Uneven thickness of film / skin or warping not close to the plate will lead to uneven absorption of laser by the plate, resulting in unstable heat generation.
Heat accumulation
When the machining path involves multiple small-size shapes, the heat will accumulate continuously as the cutting proceeds, and it is easy to burn when cutting to the second half.
Overheat at sharp corners
Overburning at sharp corners is usually caused by heat accumulation, specifically because the temperature at the sharp corners has risen to a high level when the laser passes. If the forward speed of the laser beam is greater than the heat transfer speed, overburning can be effectively avoided.
How to solve over burning?
In general, the heat conduction velocity during overburning is 2m/min, and when the cutting speed is greater than 2m/min, melting loss basically does not occur. Therefore, using high-power laser cutting can effectively prevent overheating.