Principle of wire bonding machine


Wire bonding machine generally refers to ultrasonic wire bonding machine, which is a special method of connecting the same or different metals using the mechanical vibration energy of ultrasonic frequency. When metal is subjected to ultrasonic welding, neither current is supplied to the workpiece nor a high-temperature heat source is applied to the workpiece. Instead, the vibration energy is converted into friction between the workpieces, that causes limited heating of the welding surface metal and plastic deformation. In the early stage of welding, the oxide film and impurities in the welding area are eliminated, and under a certain static pressure, the two metals are bonded together, achieving a firm welding. The metal bonding between joints is a solid-state welding achieved without melting the material, thus effectively overcoming phenomena such as splashing and oxidation generated during welding. Ultrasonic wire bonding machine can perform single point welding and multi-point welding on fine wires of non-ferrous metals such as gold, silver, copper, aluminum, nickel, etc.
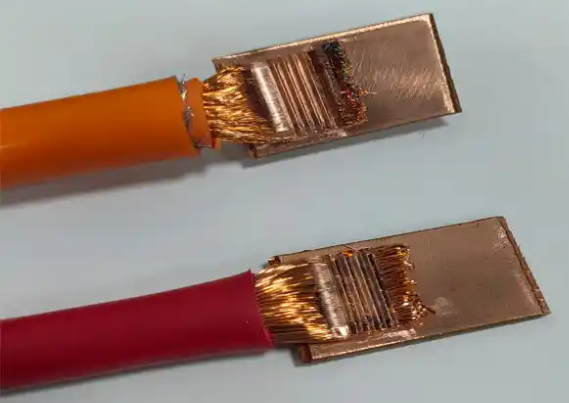
Advantages
1. High reliability: The fully automatic welding line machine uses adjustable digital time, pressure, power, temperature, arc shape, and high-precision CCD video capture to ensure that each welding point and arc shape achieves the most ideal welding effect.
2. Cost savings: One person can operate multiple machines and avoid the production of many defective products and material waste when using manual wire bonding machines. Effectively saving labor costs.
3. Low energy consumption: The energy required for a fully automatic wire bonding machine is equivalent to that of a regular manual wire bonding machine.
4. Machine lifespan: The fully automatic wire bonding machine uses high-quality imported accessories and precision machined parts, with excellent wear resistance, easy installation, high welding accuracy, and effectively extend machine lifespan.
5. High efficiency: Welding speed is several times faster than traditional manual wire welding machines.
6. Automation: With its small size, low maintenance workload, and strong adaptability, the fully automatic wire bonding machine has become the preferred choice for LED automated packaging production lines.
7. After welding, the conductivity is good, and the resistance coefficient is extremely low or almost zero.
8. Low requirements for welding metal surfaces, both oxidation and electroplating can be used for welding.
9. Short welding time, no need for any flux, gas, or solder.
10. Welding without sparks, environmentally friendly and safe.
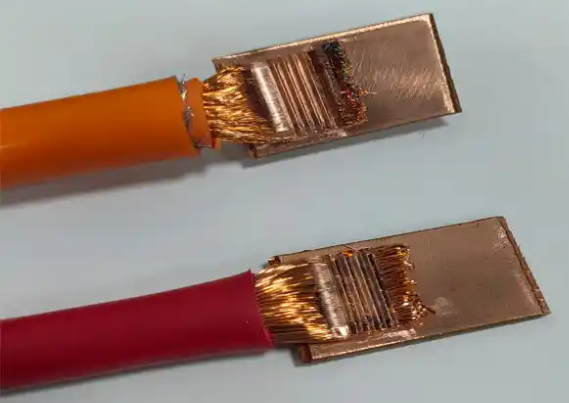
Advantages
1. High reliability: The fully automatic welding line machine uses adjustable digital time, pressure, power, temperature, arc shape, and high-precision CCD video capture to ensure that each welding point and arc shape achieves the most ideal welding effect.
2. Cost savings: One person can operate multiple machines and avoid the production of many defective products and material waste when using manual wire bonding machines. Effectively saving labor costs.
3. Low energy consumption: The energy required for a fully automatic wire bonding machine is equivalent to that of a regular manual wire bonding machine.
4. Machine lifespan: The fully automatic wire bonding machine uses high-quality imported accessories and precision machined parts, with excellent wear resistance, easy installation, high welding accuracy, and effectively extend machine lifespan.
5. High efficiency: Welding speed is several times faster than traditional manual wire welding machines.
6. Automation: With its small size, low maintenance workload, and strong adaptability, the fully automatic wire bonding machine has become the preferred choice for LED automated packaging production lines.
7. After welding, the conductivity is good, and the resistance coefficient is extremely low or almost zero.
8. Low requirements for welding metal surfaces, both oxidation and electroplating can be used for welding.
9. Short welding time, no need for any flux, gas, or solder.
10. Welding without sparks, environmentally friendly and safe.