The differences between laser soldering and wave soldering


In recent years, with the quick and continuous development of laser industry and its high reliability and low consumption, laser has replaced sorts of traditional industrial equipments.
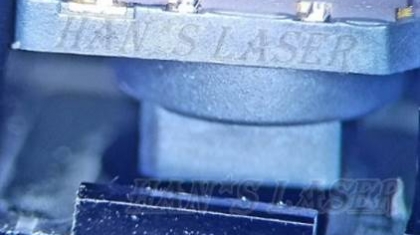
Advantages of wave soldering:
A type of through-hole component substrate welding with high production efficiency, high degree of automation, precise control of flux spraying position and amount, precise control of microwave peak height, precise control of welding position, nitrogen protection of microwave peak surface, and optimization of process parameters for each welding point. At the same time, it also combines the technology of quick replacement of nozzles of different sizes, fixed-point welding of one solder joint, and ordered array welding of through hole connector pins.
Disadvantages of wave soldering:
The PCB assembly process is only suitable for through-hole design, while SMT and CABLE WIRES are not suitable, so the application scope is limited. Due to the use of soldering flux and the generation of tin slag during welding, the later production cost is higher.
Features of laser soldering:
1. Multi-axis servo motor card control, high positioning precision.
2. Small laser beam and welding tray, tiny gap between units.
3. Good welding beam consistency, excellent appearance.
4. No soldering residues, flux waste, and lower production costs
5. The types of products that can be soldered are SMD, PTH, and cables
6. High tin penetration rate (over 90%), easy to control
7. Easy to achieve automation
8. It can accurately control the amount of tin wire fed and effectively control the usage of consumables
9. Non-contact welding, no mechanical stress and static electricity hazard
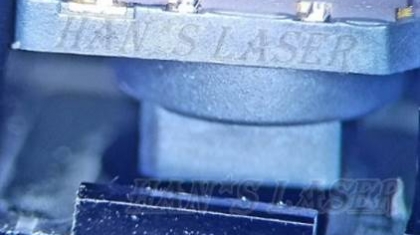
Advantages of wave soldering:
A type of through-hole component substrate welding with high production efficiency, high degree of automation, precise control of flux spraying position and amount, precise control of microwave peak height, precise control of welding position, nitrogen protection of microwave peak surface, and optimization of process parameters for each welding point. At the same time, it also combines the technology of quick replacement of nozzles of different sizes, fixed-point welding of one solder joint, and ordered array welding of through hole connector pins.
Disadvantages of wave soldering:
The PCB assembly process is only suitable for through-hole design, while SMT and CABLE WIRES are not suitable, so the application scope is limited. Due to the use of soldering flux and the generation of tin slag during welding, the later production cost is higher.
Features of laser soldering:
1. Multi-axis servo motor card control, high positioning precision.
2. Small laser beam and welding tray, tiny gap between units.
3. Good welding beam consistency, excellent appearance.
4. No soldering residues, flux waste, and lower production costs
5. The types of products that can be soldered are SMD, PTH, and cables
6. High tin penetration rate (over 90%), easy to control
7. Easy to achieve automation
8. It can accurately control the amount of tin wire fed and effectively control the usage of consumables
9. Non-contact welding, no mechanical stress and static electricity hazard