Introduction of laser welding methods: Frame welding and synchronized welding


At present, many products(including automobile semi-conductors, medical and food industries) have extremely high requirements for processing precision and cosmetic, that made laser welding has been become the necessary process of those products, also make laser welding a further development. The closer the compatibility, fusion temperature, and matching of plastic laser welding are, the better its effect will be. The application method of plastic laser welding is different from that of metal welding

1. Contour welding
The laser moves along the contour line of the plastic welding layer and causes it to melt, gradually bonding the plastic layer together; Alternatively, the interlayer can be moved along a fixed laser beam for welding purposes.
In practical applications, contour welding has high requirements for the quality of injection molded parts, especially for applications with complex welding lines such as oil and gas separators. Contour welding can achieve a certain penetration depth of the welding line in the process of plastic laser welding, but this penetration depth is small and uncontrollable, which requires that the deformation of the injection molded parts should not be too large.
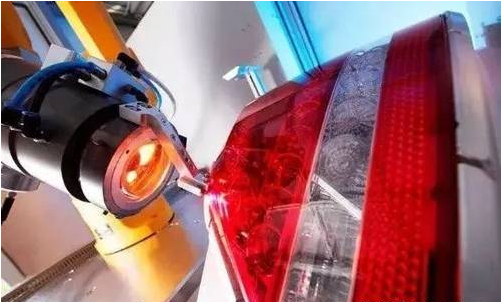
2. Synchronous welding
The laser beam from multiple diode lasers is shaped by optical elements, and the laser beam is guided along the contour line of the welding layer. At the same time, heat is generated at the weld seam, causing the entire contour line to melt and bond together simultaneously.
Synchronous welding is mainly used in the automotive light and medical industries. It is a multi-beam, optically reshaped spot that presents a welding trajectory, characterized by reducing internal stress. Due to the high requirements and overall high prices, it is widely used in the medical field temporarily.

1. Contour welding
The laser moves along the contour line of the plastic welding layer and causes it to melt, gradually bonding the plastic layer together; Alternatively, the interlayer can be moved along a fixed laser beam for welding purposes.
In practical applications, contour welding has high requirements for the quality of injection molded parts, especially for applications with complex welding lines such as oil and gas separators. Contour welding can achieve a certain penetration depth of the welding line in the process of plastic laser welding, but this penetration depth is small and uncontrollable, which requires that the deformation of the injection molded parts should not be too large.
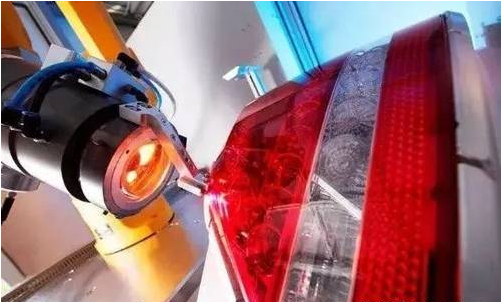
2. Synchronous welding
The laser beam from multiple diode lasers is shaped by optical elements, and the laser beam is guided along the contour line of the welding layer. At the same time, heat is generated at the weld seam, causing the entire contour line to melt and bond together simultaneously.
Synchronous welding is mainly used in the automotive light and medical industries. It is a multi-beam, optically reshaped spot that presents a welding trajectory, characterized by reducing internal stress. Due to the high requirements and overall high prices, it is widely used in the medical field temporarily.