The laser application in sensors


Sensor has integrated the sensing chips, telecommunication chips, microprocessors, drivers and software algorithm in one, it has the information collection, processing, exchange and memory functions.
With the development of laser and automation technology as well as the mature application in sensor production process, those companies that grasped the laser welding key technology are further solving the bad accuracy and poor stability and so on problems of sensors, playing an important role in the meantime.
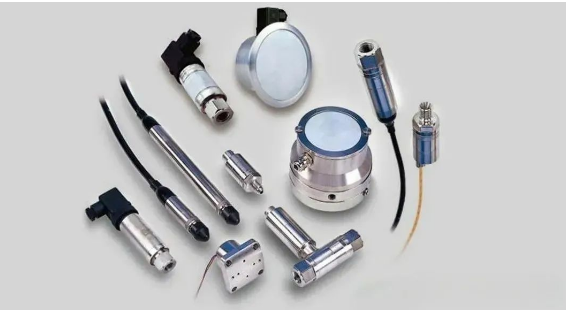
The advantages of laser welding
Compared to traditional arc welding processes, laser welding has many advantages:
1. Selective energy application in small areas: reducing thermal stress and reducing heat affected zone, with extremely low distortion.
2. Narrow joint seam and smooth surface
3. Combination of high strength and low welding volume: The welded workpiece can withstand bending or hydraulic forming.
4. Easy to integrate: can be combined with other production operations, such as alignment or bending.
5. Only one side of the seam
6. High working speed reduces processing time.
7. Especially suitable for automation technology.
8. Good program control: Machine tool control and sensor system detect process parameters and ensure quality.
9. Laser beams can generate solder joints without touching the surface of the workpiece or applying force to the workpiece.
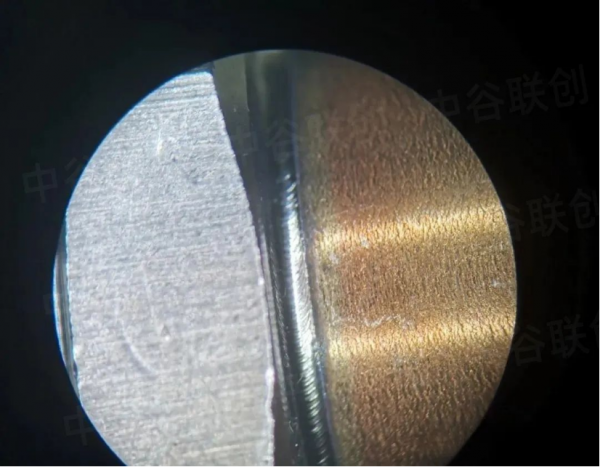
Laser welding process for sensors
Sensors, as high-precision detection instruments, have extremely strict requirements especially in military, aviation, and aerospace applications. To develop and produce sensors with high accuracy and stability, a complete and effective manufacturing process is essential. Why do we say that? The main reason is that sensors such as pressure sensors, Hall sensors, photoelectric sensors, temperature sensors, etc. have sensitive components and integrated circuits inside, which are filled with inert gas or vacuum isolated from the outside world. The production process requires pressure resistance and airtightness, and high requirements for welding strength, gas leakage rate, and welding quality. Especially during the welding process, small deformation is required, and internal components and microcircuits cannot be damaged.
Laser welding uses laser as the welding heat source, which has advantages such as high energy density, concentrated heating, fast welding speed, and small welding deformation. Due to the current use of stainless steel, titanium alloys, as well as a small amount of alloy materials and aluminum alloys in the shells of various sensors, laser welding is particularly suitable for use in sensor sealing welding due to its unique advantages.
With the development of laser and automation technology as well as the mature application in sensor production process, those companies that grasped the laser welding key technology are further solving the bad accuracy and poor stability and so on problems of sensors, playing an important role in the meantime.
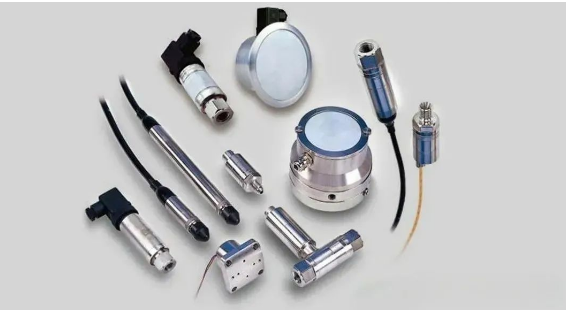
The advantages of laser welding
Compared to traditional arc welding processes, laser welding has many advantages:
1. Selective energy application in small areas: reducing thermal stress and reducing heat affected zone, with extremely low distortion.
2. Narrow joint seam and smooth surface
3. Combination of high strength and low welding volume: The welded workpiece can withstand bending or hydraulic forming.
4. Easy to integrate: can be combined with other production operations, such as alignment or bending.
5. Only one side of the seam
6. High working speed reduces processing time.
7. Especially suitable for automation technology.
8. Good program control: Machine tool control and sensor system detect process parameters and ensure quality.
9. Laser beams can generate solder joints without touching the surface of the workpiece or applying force to the workpiece.
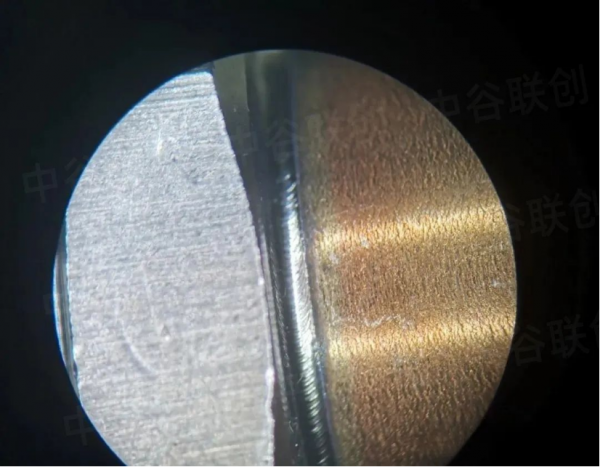
Laser welding process for sensors
Sensors, as high-precision detection instruments, have extremely strict requirements especially in military, aviation, and aerospace applications. To develop and produce sensors with high accuracy and stability, a complete and effective manufacturing process is essential. Why do we say that? The main reason is that sensors such as pressure sensors, Hall sensors, photoelectric sensors, temperature sensors, etc. have sensitive components and integrated circuits inside, which are filled with inert gas or vacuum isolated from the outside world. The production process requires pressure resistance and airtightness, and high requirements for welding strength, gas leakage rate, and welding quality. Especially during the welding process, small deformation is required, and internal components and microcircuits cannot be damaged.
Laser welding uses laser as the welding heat source, which has advantages such as high energy density, concentrated heating, fast welding speed, and small welding deformation. Due to the current use of stainless steel, titanium alloys, as well as a small amount of alloy materials and aluminum alloys in the shells of various sensors, laser welding is particularly suitable for use in sensor sealing welding due to its unique advantages.