Technological advantages of laser welding machine in welding ultra-thin materials


The traditional welding machine has one big difficulty for processing the SUS thin plate, due to the low thermal conductivity and constraints of SUS thin plate, once subjected to local heating and cooling during the welding process, uneven stress and strain will be formed. The longitudinal contraction of the weld seam generates a certain pressure on the outer edge of the stainless steel plate. Once the pressure is too high, traditional welding machines will cause wavy deformation of the workpiece, Not only does it affect the aesthetics, but it also affects the quality of the workpiece, and in addition, there may be issues of over burning and burning through. The fiber laser welding machine solves this problem. Laser welding uses high-energy laser pulses to heat materials locally in a small range.
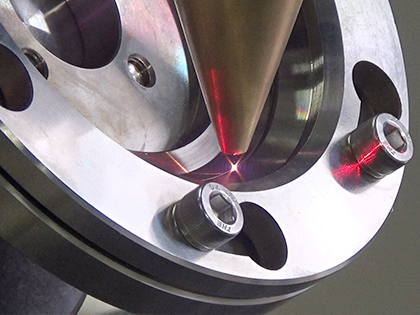
Compared with other welding machines, metal laser welding machine has the advantage of wide application range, which can be widely used for welding stainless steel, metal, alloy and other same materials, and can also realize welding of different materials; What are the process advantages of laser welding machine in welding ultra-thin materials?
Technological advantages of laser welding machine in welding ultra-thin materials:
1. Laser welding machine is easy to cooperate with computer numerical control system or manipulator and robot to realize automatic welding and improve production efficiency.
2. Laser processing welding is non-contact processing, without issues such as tool wear and tool replacement. The laser beam energy is adjustable, the movement speed is adjustable, and it can be used for various welding processes.
3. Laser welding can be controlled by computer, with fast welding speed and high efficiency. It is convenient to weld any complex shape.
4. The welding process does not pollute the environment and can be directly welded in the air, making the process simple.
5. The welding spot is small, the weld seam is narrow, neat and beautiful, and there is no need for processing or only a simple processing process after welding.
6. Because the light beam is easy to transmit and control, and there is no need to frequently replace the welding torch and nozzle, significantly reducing the auxiliary downtime, the load factor and production efficiency are both high.
7. Easy to achieve automation, effective control of beam intensity and precise positioning.
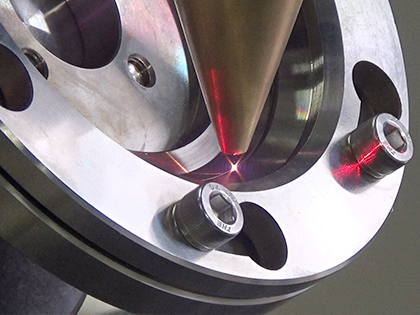
Compared with other welding machines, metal laser welding machine has the advantage of wide application range, which can be widely used for welding stainless steel, metal, alloy and other same materials, and can also realize welding of different materials; What are the process advantages of laser welding machine in welding ultra-thin materials?
Technological advantages of laser welding machine in welding ultra-thin materials:
1. Laser welding machine is easy to cooperate with computer numerical control system or manipulator and robot to realize automatic welding and improve production efficiency.
2. Laser processing welding is non-contact processing, without issues such as tool wear and tool replacement. The laser beam energy is adjustable, the movement speed is adjustable, and it can be used for various welding processes.
3. Laser welding can be controlled by computer, with fast welding speed and high efficiency. It is convenient to weld any complex shape.
4. The welding process does not pollute the environment and can be directly welded in the air, making the process simple.
5. The welding spot is small, the weld seam is narrow, neat and beautiful, and there is no need for processing or only a simple processing process after welding.
6. Because the light beam is easy to transmit and control, and there is no need to frequently replace the welding torch and nozzle, significantly reducing the auxiliary downtime, the load factor and production efficiency are both high.
7. Easy to achieve automation, effective control of beam intensity and precise positioning.