Comparison of glass cutting processes, advantages of ultrafast laser glass cutting


Comparison of glass cutting process
Traditional cutting tool glass cutting
The traditional glass cutting process includes knife wheel cutting and CNC grinding cutting. The glass cut by the cutter wheel has large edge collapse and rough edge, which will greatly affect the strength of the glass. Moreover, the glass yield of the cutter wheel is low as well as the material utilization rate. After cutting, the post-treatment of complex processes is also needed. When the cutter wheel is used for special-shaped cutting, the speed and accuracy will be greatly reduced. Some special-shaped screens cannot be cut with the cutter wheel because the corner is too small. CNC has higher accuracy than cutter wheel, with accuracy ≤ 30 μm. The edge collapse is smaller than the cutter wheel, about 40 μm. However, the disadvantage of CNC is the slow speed.
Traditional laser glass cutting
Laser cutting has the advantages of high speed, high precision, no burr and no shape limitation, and the edge collapse is generally less than 80 μm。 Because the glass is fragile, the laser beam with high overlap rate will accumulate excessive heat on the glass and crack the glass surface. Therefore, the laser cannot use the beam with high overlap rate for one-time cutting. Generally, the galvanometer is used for high-speed scanning to remove the glass layer by layer, and the general cutting speed is less than 1mm / s.
Ultrafast laser glass cutting
In recent years, ultrafast laser (or ultrashort pulse laser) has made rapid development, especially in the application of glass cutting, which has achieved very excellent performance. It can avoid the problems of edge collapse and crack in traditional machining cutting. It has the advantages of high precision, no microcrack, breakage or debris, high edge fracture resistance, no washing, polishing and other advantages of secondary manufacturing cost, reduce the cost and greatly improve the workpiece yield and processing efficiency.
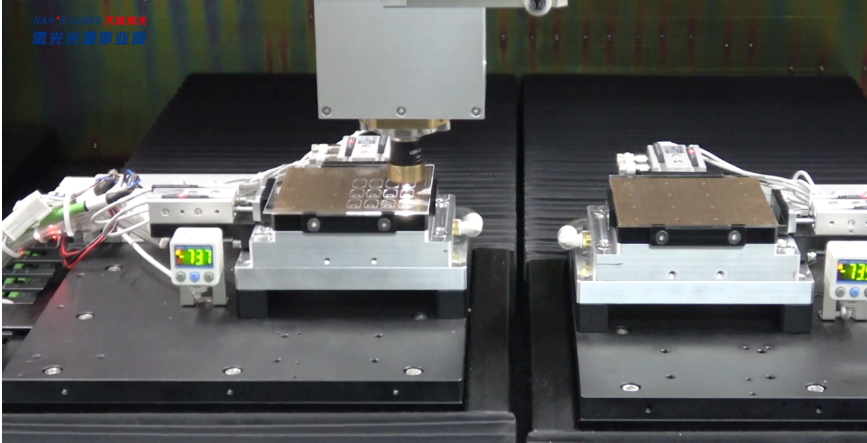
Traditional cutting tool glass cutting
The traditional glass cutting process includes knife wheel cutting and CNC grinding cutting. The glass cut by the cutter wheel has large edge collapse and rough edge, which will greatly affect the strength of the glass. Moreover, the glass yield of the cutter wheel is low as well as the material utilization rate. After cutting, the post-treatment of complex processes is also needed. When the cutter wheel is used for special-shaped cutting, the speed and accuracy will be greatly reduced. Some special-shaped screens cannot be cut with the cutter wheel because the corner is too small. CNC has higher accuracy than cutter wheel, with accuracy ≤ 30 μm. The edge collapse is smaller than the cutter wheel, about 40 μm. However, the disadvantage of CNC is the slow speed.
Traditional laser glass cutting
Laser cutting has the advantages of high speed, high precision, no burr and no shape limitation, and the edge collapse is generally less than 80 μm。 Because the glass is fragile, the laser beam with high overlap rate will accumulate excessive heat on the glass and crack the glass surface. Therefore, the laser cannot use the beam with high overlap rate for one-time cutting. Generally, the galvanometer is used for high-speed scanning to remove the glass layer by layer, and the general cutting speed is less than 1mm / s.
Ultrafast laser glass cutting
In recent years, ultrafast laser (or ultrashort pulse laser) has made rapid development, especially in the application of glass cutting, which has achieved very excellent performance. It can avoid the problems of edge collapse and crack in traditional machining cutting. It has the advantages of high precision, no microcrack, breakage or debris, high edge fracture resistance, no washing, polishing and other advantages of secondary manufacturing cost, reduce the cost and greatly improve the workpiece yield and processing efficiency.
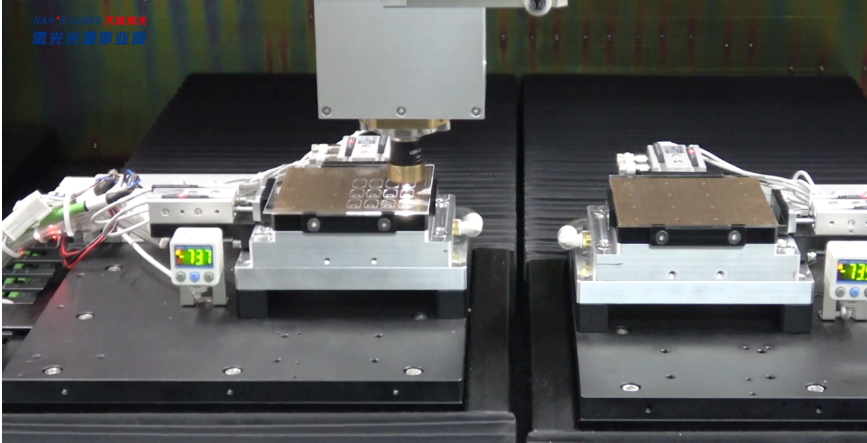